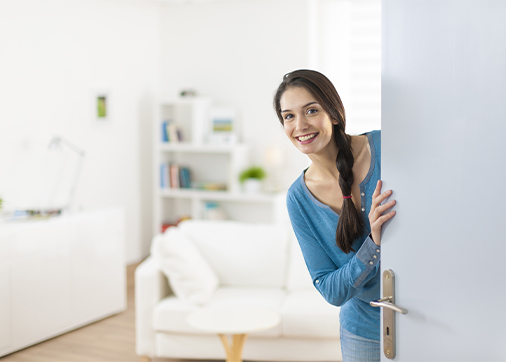
AK/APPLE PARTICLE BOARD FLUSH DOOR
AK/Apple waterproof Particleboard Flush Doors are manufactured from selected, well-seasoned vacuum pressure treated (VPT) hardwood timber/ Pine timber and particle board which conforms to IS 3087. We are using Sylvester pine which is naturally resistant to borer & termites and is far superior to any other pine species. The Particleboard is framed with finger jointed (As per BIS specification) seasoned hardwood battens (Stile & rail)/ Pinewood battens (stile & rail) strengthened by a layer of cross bands, and face veneers that confine both sides of the core. All these are bonded at high pressure & temperature with phenol formaldehyde resin and permanent type of preservatives. This process ensures maximum insulation against heat, dust, and noise. A variety of sizes are available, ranging from 25mm to 55mm in thickness. This is a superior IS 2202 and ISO 9001 certified product.
DOORS
FEATURES

Panel sizes :
A range of sizes are available according to customer needs.

Thickness :
Common thickness range from 25mm to 45mm.

Bond/Adhesive :
Phenol formaldehyde (PF) for weather and Boil Water Proof (BWP) and low formaldehyde formulation for compliance to emission level requirements such as E1.

Standard :
Conforms to Indian standards, IS 2202 (Bureau of Indian Standards) is produced in compliance with internationally recognised standards such as (An ISO 9001 certified company).
Benefits
1) Dimensional stable core signifying enhanced strength and extra durability.
2) Its frames provide strength for fitting of hinges and anti deviation resistance.
3) Chemically treated to resist borer and termite attack.
4) Kiln dried to resist moisture, warping and to avoid twisting.
5) Manufactured to suit local climate and ready onto fix doors.
6) Excellent strength, stiffness impact resistance
7) Unique dimension stability
8) Superior finish.
TECHNICAL INFORMATION AS PER IS 2202
SL. No | TESTS | SIZE OF SPECIMEN | PRESCRIBED VALUE | OBSERVED VALUE |
---|
1 | Dimensions,mm & Squareness | Full size door | Height- ± 5 mm Width- ± 5 mm Thickness- ± 1 mm Squareness – Not more than 1 mm on a length of 500 mm |
+0 +0 +0.40
0.50 |
2 | General Flatness | Full size door | Twist,cupping & warping shall not exceed 6 mm | Twist-2.5 Cupping-1.9 Warping-1.8 |
3 | Local plainness | Full size door | Depth of deviation shall not be more than 0.5 mm | 0.08 |
4 | Impact indentation | Full size door | Depth of deviation shall not be more than 0.2 mm | 0.11 |
5 | Flexure (mm) 15 mints after loading 50kg | Full size door | Deflection shall not be more than 1/30 of length or 1/15 of width whichever is less. | 44.00 |
3 mins after load removal | Residual deflection shall not be more than 1/10 of max deflection. | 2.80 | ||
6 | Edge loading(mm) After 15min of 100 kg loading. | Full size door | Deflection shall not be more than 5 mm. | 3.60 |
3 min after load removal lateral buckling | Residual deflection shall not be more than 0.5 mm. | 0.22 | ||
No lateral buckling by more than 2 mm during loaded. No residual lateral buckling after removal | 1.10 No lateral buckling |
|||
7 | Shock resistance Test Soft & light body impact
Soft & heavy body impact |
Full size door | No visible damage.
No visible damage. |
No visible damage.
No visible damage. |
8 | Buckling(mm) After 5min of 40 kg loading. | Full size door | Initial deflection shall not be more than 50 mm. | 41.00 |
After 15 mints of unloading | No deterioration Residual deformation shall not more than 5 mm. | No deterioration. 2.90 |
||
9 | Slamming Test | Full size door | Shall not have any visible damage in any part of the door | No visible damage. |
10 | Misuse test | Full size door | Shall not be any permanent deformation of the fixing or any other part of the doorset | No permanent deformation. |
11 | End immersion test | Full size door | No delamination | No delamination |
12 | Knife test | Full size door | Minimum Pass standard | Excellent |
13 | Glue adhesion test | 150mmx150mm from the two corners of the door | No delamination | No delamination |
14 | Screw withdrawal strength, | 150mm X 75mm | Not less than 1000 N | 1310 |
ADVANTAGES OF FINGER JOINT: (AS PER BIS SPECIFICATION)
Finger jointing results in higher quality and stronger pieces and components, while dramatically reducing waste in the industry. By using finger joints, it is possible to produce pieces of sawn timber that are made completely of heartwood, knotless and very straight. The most important advantages of finger joint wood are straightness, dimensional stability, and the end product is always of premium quality.
INSTALLATIONS & STORAGE GUIDELINES FOR FLUSH DOOR-
1) Deliver doors to the building site after the plaster, drywall and/or concrete dries.
2) Stacking of flush doors are recommended to be in a horizontal position on a flat floor in a clean, dry, well-ventilated building; the doors shall be kept away from direct sunlight and source of extreme heat, cold or humidity. Do not lean on the doors vertically against a wall or other structure.
3) If the doors are being stored at the job site and not for immediate installation, the top & bottom sides must be sealed.
4) Flush doors should not be trimmed by more than 10mm at any of its edges.
5) Locks should be placed at exactly the place shown by the sticker, immediately after the installation.
6) The gap between the frame and door shall be 3mm.
7) Polish/paint or laminate on door surface is recommended to be on both sides and with same characteristics material only, to avoid warpage later on.
2) Stacking of flush doors are recommended to be in a horizontal position on a flat floor in a clean, dry, well-ventilated building; the doors shall be kept away from direct sunlight and source of extreme heat, cold or humidity. Do not lean on the doors vertically against a wall or other structure.
3) If the doors are being stored at the job site and not for immediate installation, the top & bottom sides must be sealed.
4) Flush doors should not be trimmed by more than 10mm at any of its edges.
5) Locks should be placed at exactly the place shown by the sticker, immediately after the installation.
6) The gap between the frame and door shall be 3mm.
7) Polish/paint or laminate on door surface is recommended to be on both sides and with same characteristics material only, to avoid warpage later on.
STRUCTURAL IMAGE
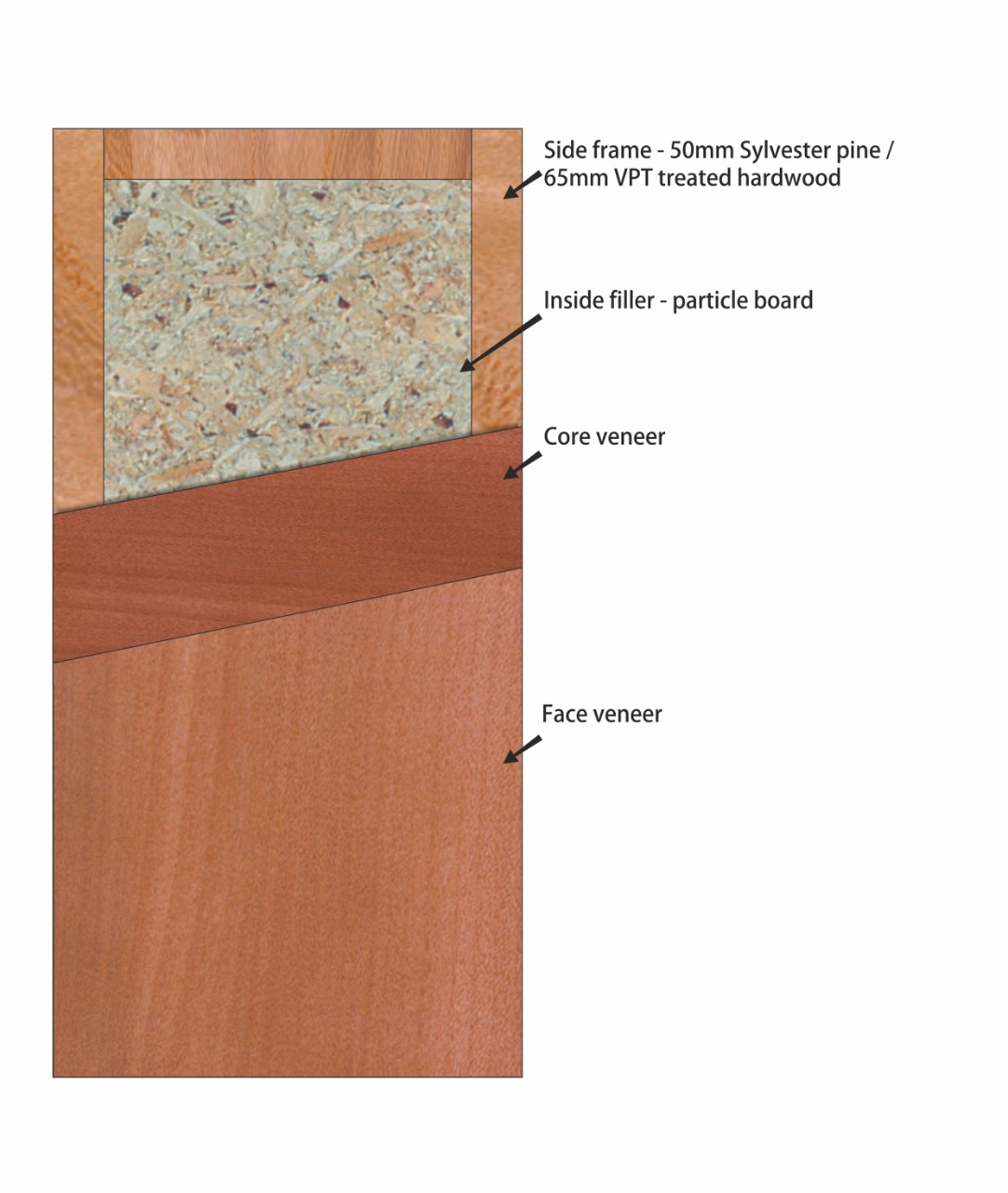